Wood plastic composites (WPCs) are a new type of composite materials that have flourished at home and abroad in recent years. They refer to the plates or profiles produced by using polyethylene, polypropylene and polyvinyl chloride instead of common resin adhesives, and mixing more than 35% - 70% of wood flour, rice husk, straw and other waste plant fibers into new wood materials, and then through extrusion, molding, injection molding and other plastic processing processes. It is mainly used in building materials, furniture, logistics packaging and other industries. Plastic and wood powder are mixed in a certain proportion and then formed by hot extrusion, which is called extruded wood plastic composite plate.
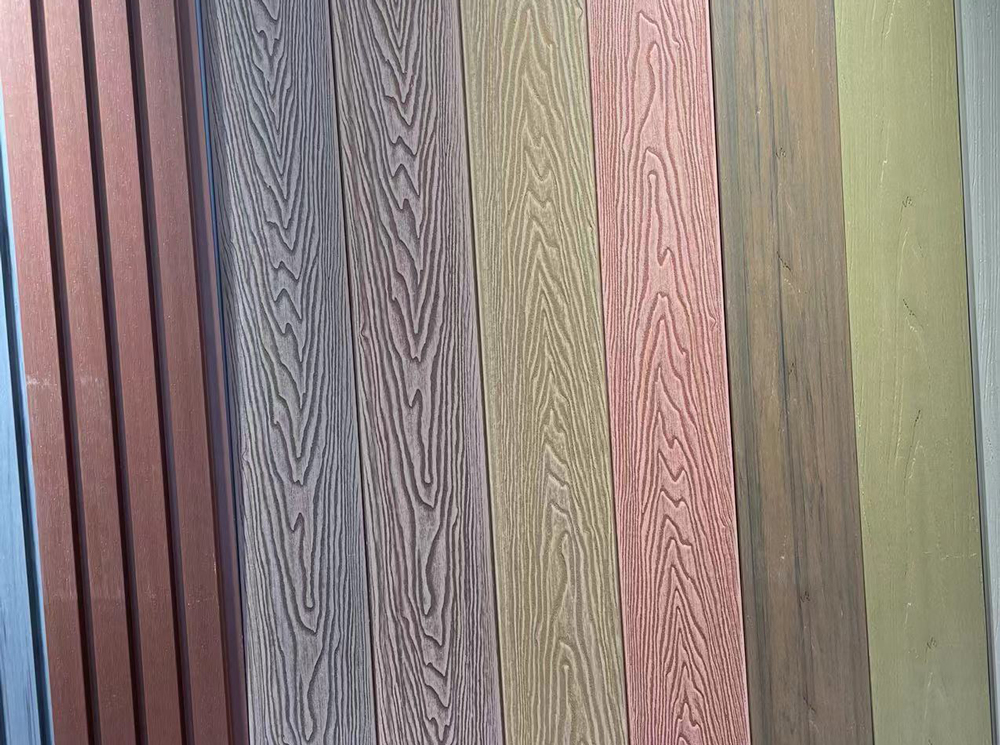
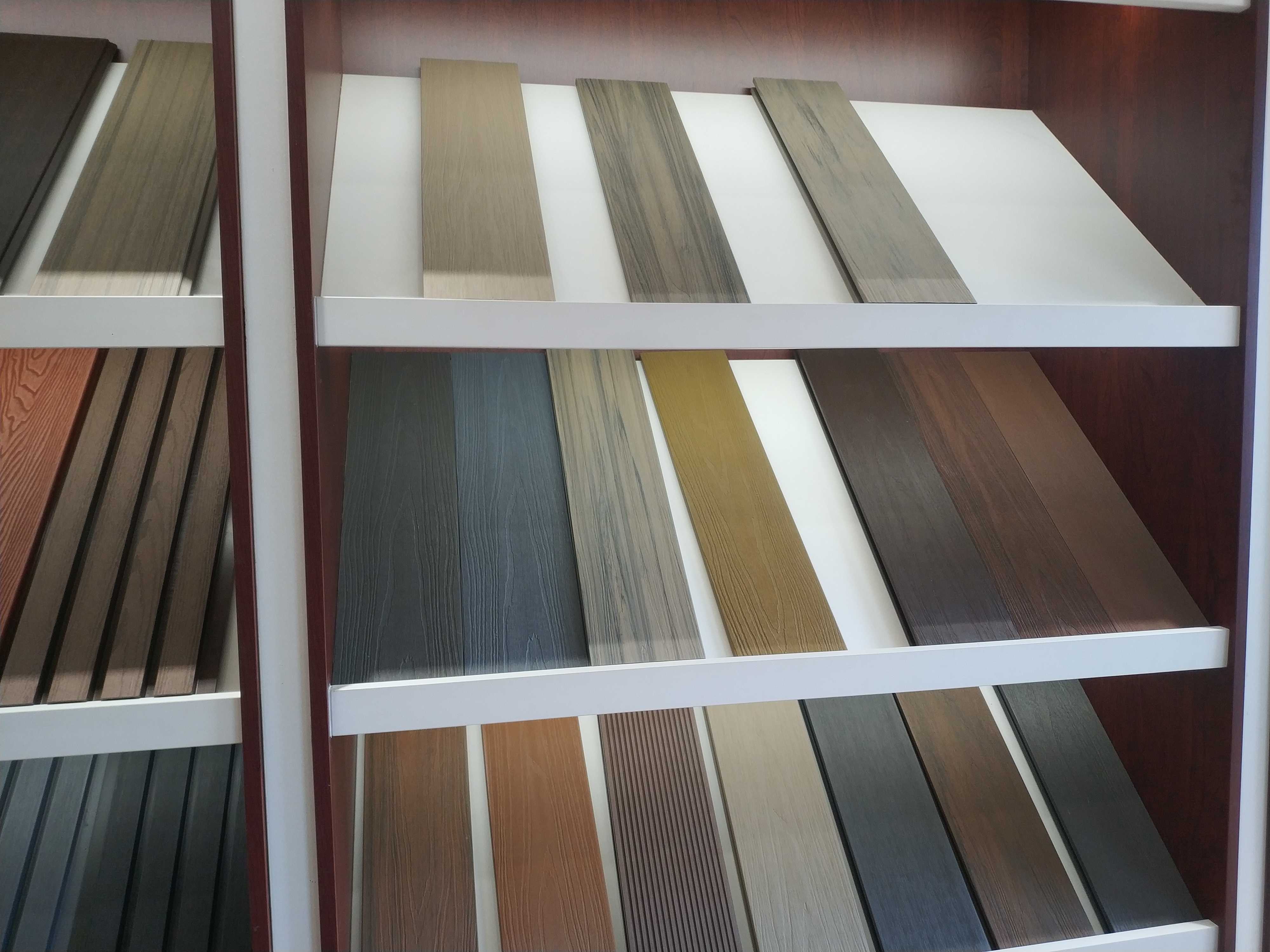
Screw configuration plays an important role in the extrusion process of wood plastic composites. The reasonable screw structure can reduce the friction between the screw and wood fiber, produce proper shearing and dispersion mixing, and make the material system containing a large amount of wood powder well plasticized.
Mold design and cooling finalization
In addition to ensuring smooth transition and reasonable flow distribution of the runner design, wood plastic composite materials have higher requirements for pressure building capacity and temperature control accuracy.
In order to obtain good fiber orientation and product quality, it is necessary to ensure that the die head has sufficient pressure building capacity and long sizing section, and even adopt double taper structure in compression section and sizing section.
Wood plastic composite materials have poor thermal conductivity, and most of its products are profiled materials, which are difficult to be cooled and shaped, so they are mostly water-cooled. The cooling channel shall be designed reasonably to ensure efficient cooling.
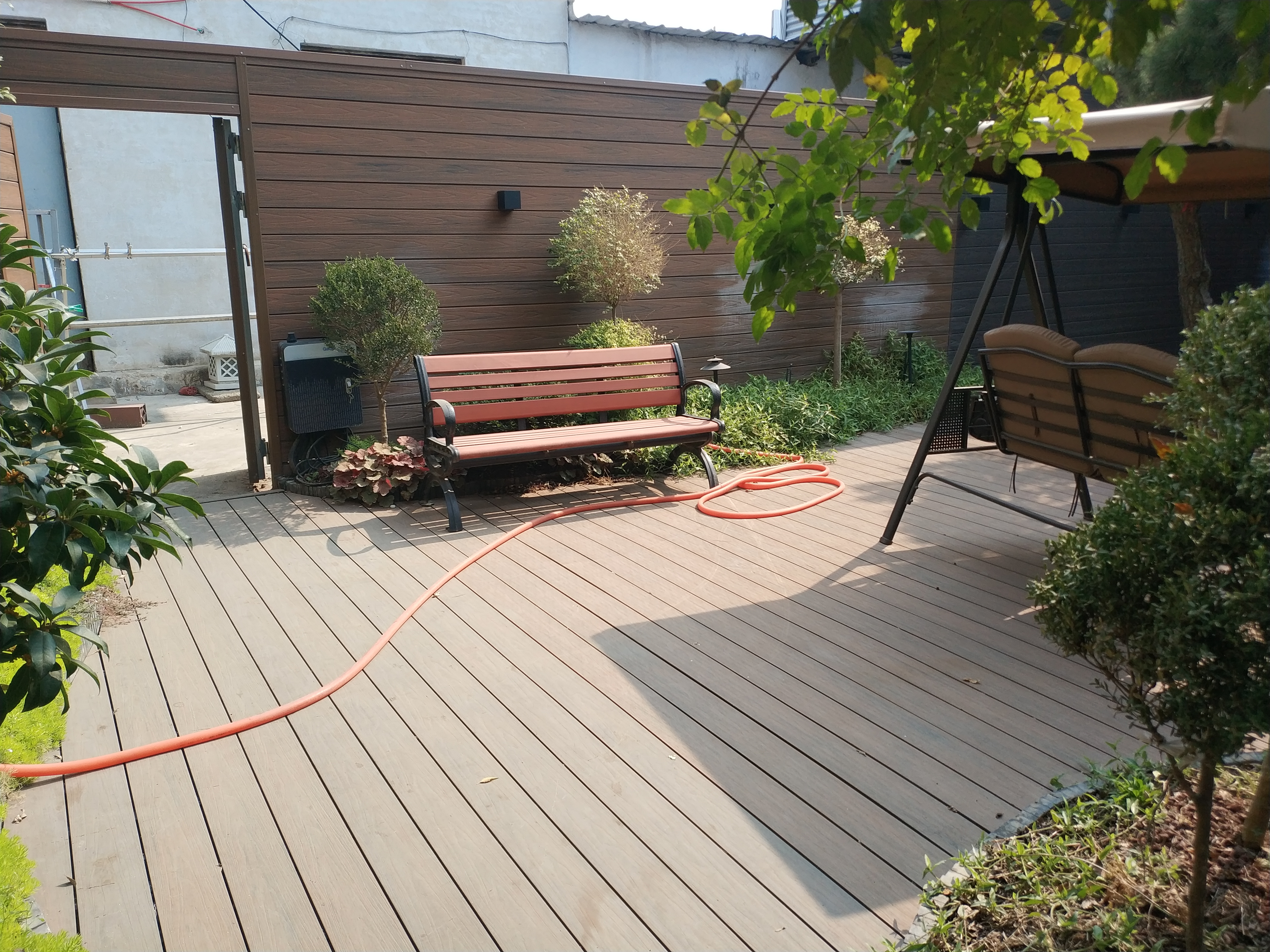
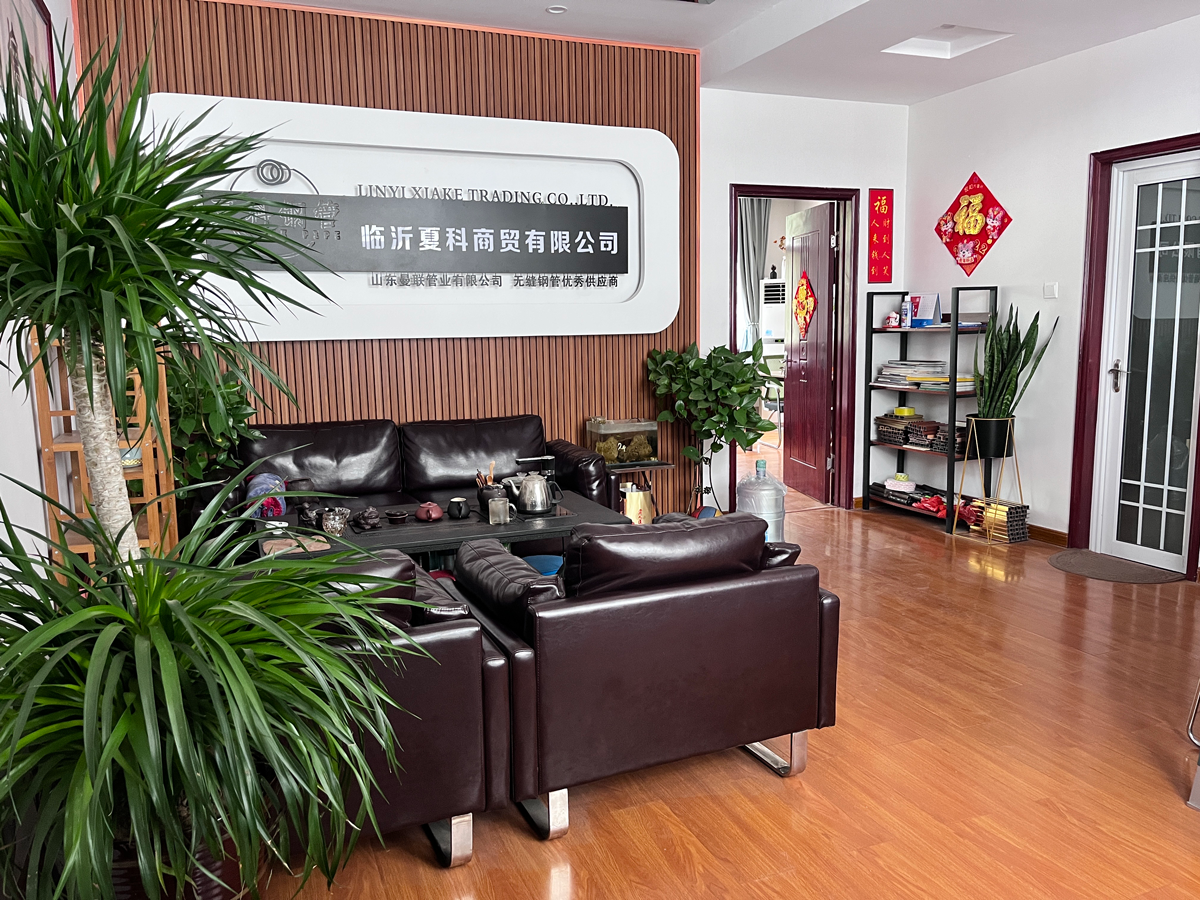
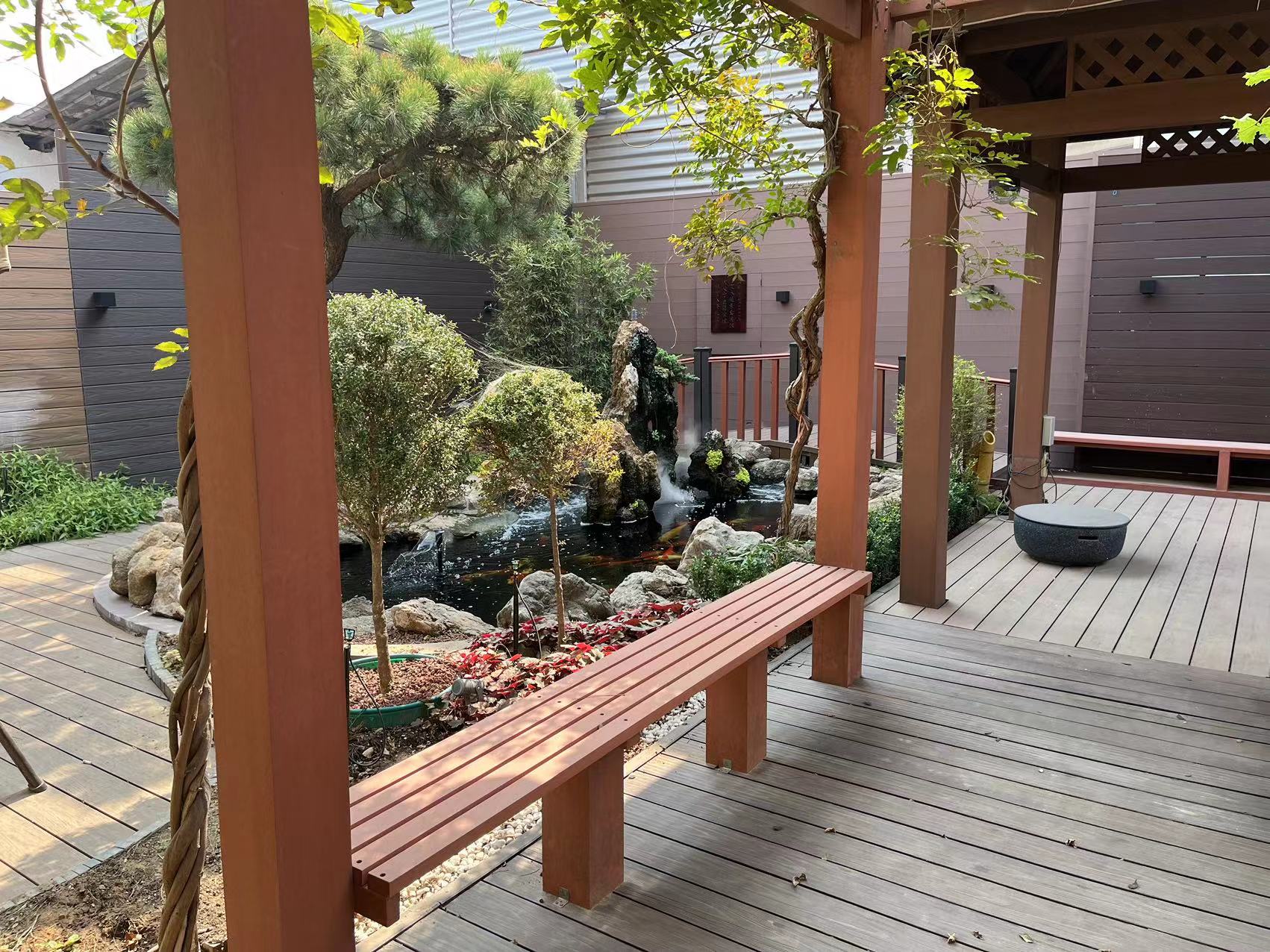
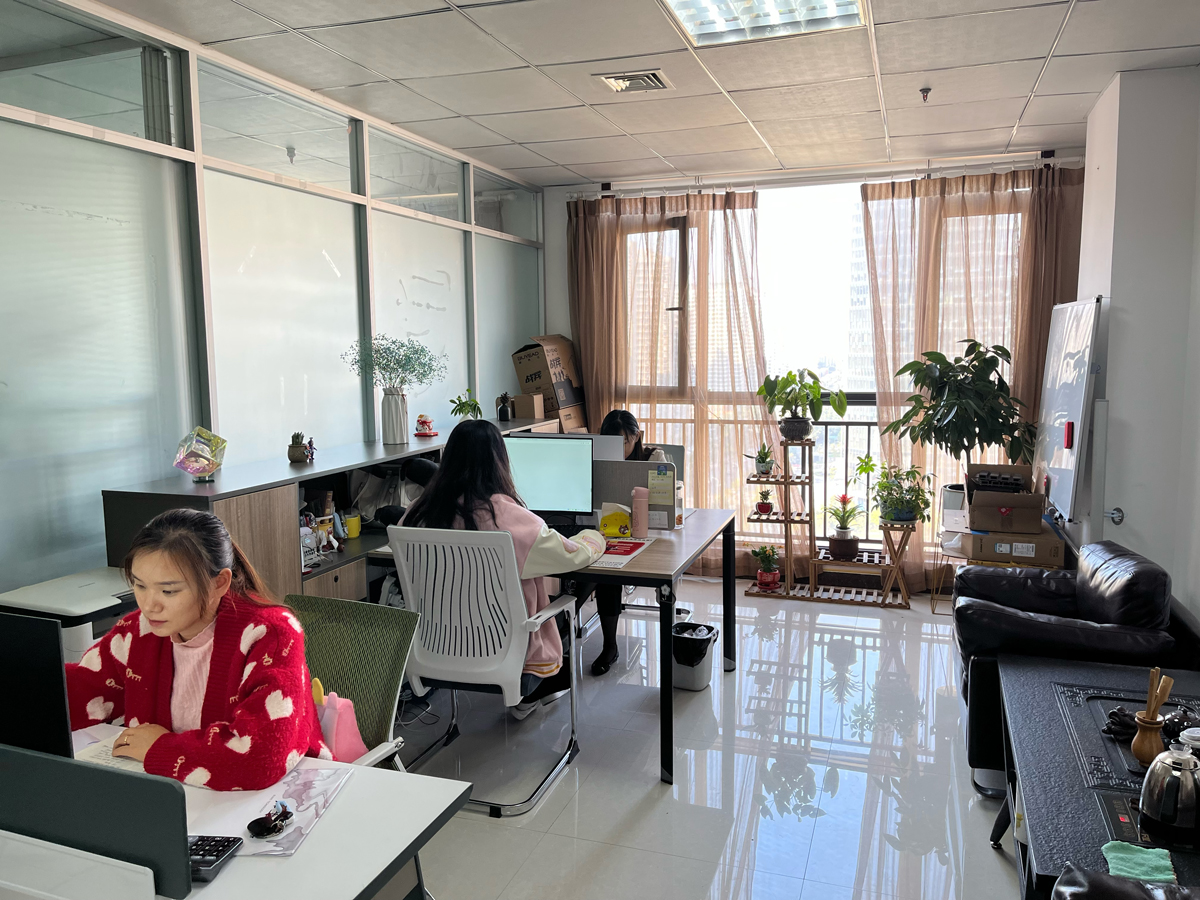